WätaS Wärmetauscher Sachsen GmbH
WätaS designs heat exchangers with the customX configuration software, whereby most variants are produced individually.
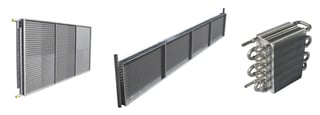
Targets
To accelerate the internal order processing using lean production while maintaining product variability. To provide capacity for further growth by ensuring fast availability of correct documents with significantly reduced effort. To be independent of external service providers.
Implementation
After the administrator had been trained, the system was set up and expanded independently at WätaS. Today, all heat exchangers are individually configured with customX. For this, customX uses the data of an individual program for the thermal calculation and automatically transfers data to ERP and production control after the configuration.
Conclusion
WätaS is particularly satisfied with two factors: On the one hand, the speed, without which it would not be possible to process so many orders, and on the other hand, the practicability of supporting and maintaining the system inhouse, which entails low costs and fast responsiveness.
Efficient individual production in ultra-modern production plant
The heat exchangers of WätaS Wärmetauscher Sachsen GmbH, headquartered in Olbernhau near the Czech border, are well-known and used in a wide variety of areas for heating, cooling and dehumidification. The number of variants produced/supplied by WätaS is correspondingly high.
Each product is unique
95 % of all heat exchangers produced at WätaS are individual pieces; the remaining 5 % are small series production. It is, therefore, not difficult to imagine how much flexibility is required in sales and production and how much preparation is needed for each heat exchanger.
Initially, WätaS produced rough, hardly usable 3D models for the quotations and then, after getting the order, manually created all the necessary drawings and models in the CAD system. About ten minutes were required just to make this first model that was not true to scale, and then it was of no further use. This situation was not viable for WätaS as they wanted to produce quickly and efficiently using lean production methods and further continue their enormous growth despite the lack of skilled workers.
Enormous time savings
The configuration software customX from the specialists of Man and Machine solved all these problems. Today, all heat exchangers are configured with customX and, after less than half a minute, not only scale models but also all detailed drawings are automatically available. This also means that any changes to the customer's requirements are no longer a problem - the new values just have to be entered and everything is ready to go.
Automated processes
When a customer requests a heat exchanger, they simply specify their requirements (e.g. available space, application area and thermal values). An individual program for structural design then generates the thermal calculations. Afterwards, these values are used by customX for the construction of the heat exchanger variant. Production can begin immediately after the customer’s approval as customX generates bills of materials as well as drawings, and transfers all data to SAP and production control.
customX convinces
On his very first contact with customX, Managing Director Torsten Enders was convinced that WätaS absolutely needed this software as it would immediately eliminate the bottlenecks in the engineering department. After the introduction of customX, the employees quickly appreciated how much easier and faster work has become. IT manager David Dostmann confirmed how important the configurator is for his company: "Without customX we could not process this mass of orders at all". He explained that, by using customX, two workplaces could be saved in modification engineering - with today's order volume, it would certainly be even more. Employees can now be deployed much more effectively in R&D.
Without customX we could not process this mass of orders at all.
David Dostmann
IT Manager,WätaS Wärmetauscher Sachsen GmbH
Do it yourself
David Dostmann is in charge of the entire customX set of rules and is pleased that after only six days of training he rarely needs the support of the customX specialists - e.g. for updates or basic function enhancements. "A huge advantage of customX is that we can do everything ourselves and are not dependent on external specialists, for whom we would have to wait and who would cause enormous costs", Mr. Dostmann is happy to say.
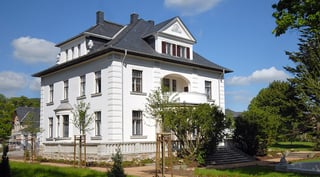
Further development
With this extremely positive experience with customX, the next step is to configure the wiring of the heat exchangers and the adaptation of the distributors via the configurator so that the whole heat exchanger connection is also automatically represented in correct, true-to-scale drawings. Great attention will be paid to the introduction of 3D.
Of course, R&D is not at a standstill either. For example, the company is working intensively on other forward-looking technologies such as the fuel cell.